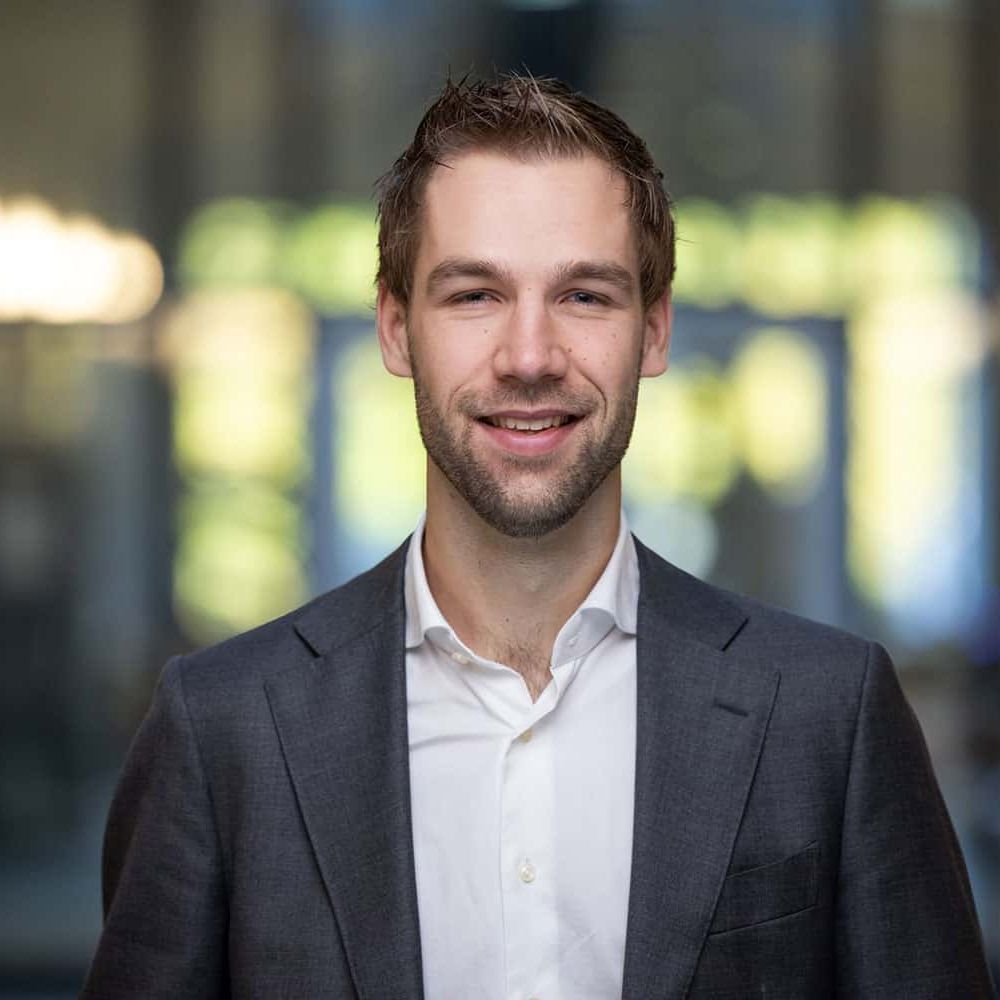
highlights
• producing radio-isotopes with minimal nuclear waste
• using liquid metal as a coolant
• running in a radiation facility with automated harvesting robots
developing the heart of this factory.
The Belgian organization IRE is one of the four largest suppliers of medical radio-isotopes on the planet. In the SMART project, IRE is developing a novel production facility for Molybdenum (Mo) 99, the ‘parent isotope’ of Tc-99m. The medically used Tc-99m has a half-life of only 6 hours. Hence, production of this isotope directly is not feasible without it decaying before it reaches the hospitals. The halftime of Mo-99, in contrast, is 66 hours, which leaves just enough room to ship it around the world. At the hospital or treatment centers, it decays into Tc-99m, which is injected for medical use.
The novel production concept is based on the LightHouse Isotopes concept. It relies on exposing a molybdenum-100 target to high-energy electrons to produce Mo-99 by releasing a neutron. A factory is being developed that will supply a large share of the global Mo-99 demand without using a nuclear reactor.
pushing what is technically possible.
The three key challenges in the SMART project arise from the high energy of the electrons and the resulting high power dissipation in the target and surroundings: How can we handle 2 Megawatts of power in a matchbox-sized target? The first issue is cooling the target. The second challenge is handling the intense radiation during exposure. It is not only deadly to humans but also causes all components in the vicinity of the target to deteriorate quickly. Third, given these challenges, how can you operate the factory reliably in a fully continuous process?
The solution of the cooling challenge is found in using liquid sodium as a coolant, which, however, comes with challenges of its own as a consequence of the highly reactive nature of this metal. The radiation issues require thick radiation shielding and as well as the meticulous selection of components and materials. The reliability challenge is tackled by using an automated harvesting process and a modular design, which facilitates component replacement based on predictive maintenance.
“using high-energy physics and engineering to reduce the radioactive waste.”
Given the novelty and complexity of the challenges, it is difficult to prove the feasibility of our design solutions for the exposure and harvesting modules. Verification experiments are mandatory to quantify the key unknowns. A central role in these experiments plays a miniature (1 in a 1000) version of the full exposure cell. We are very happy that it passed its Site Acceptance Test (SAT) at full power density successfully on the first try.
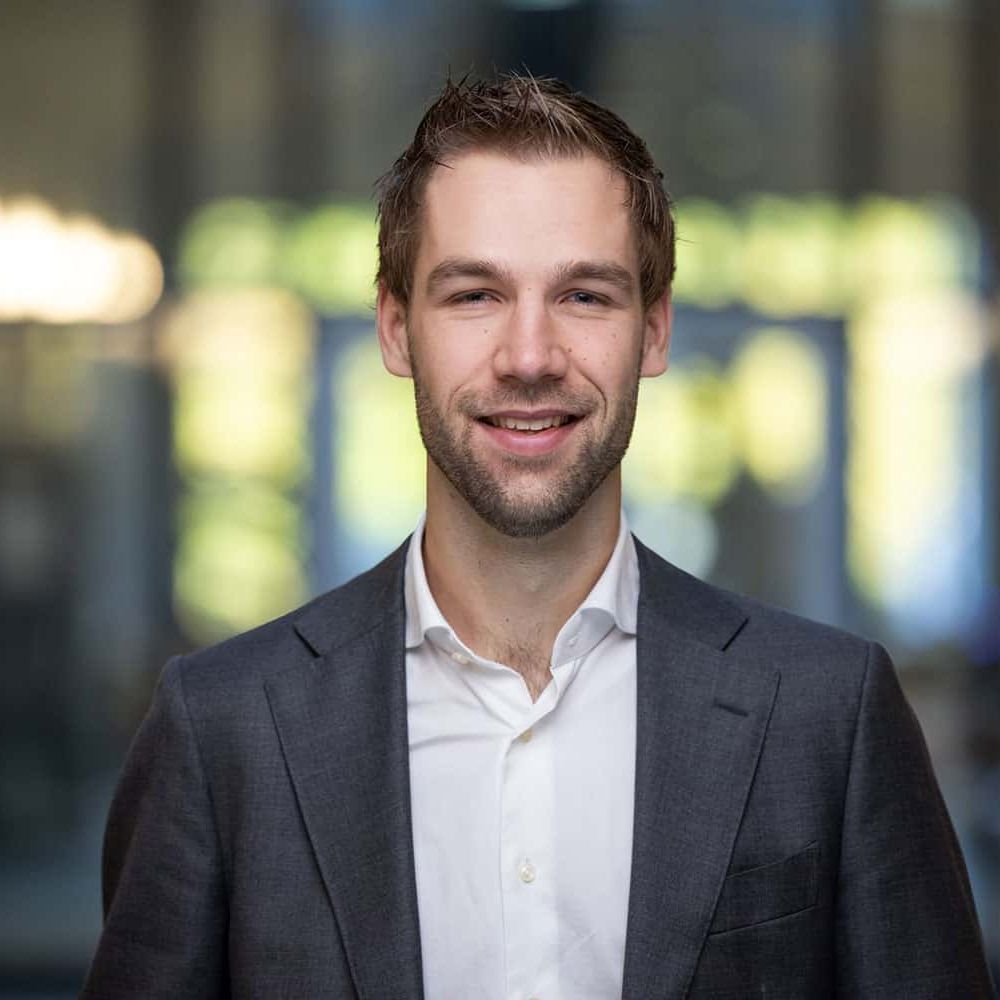